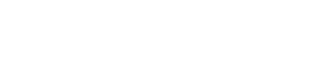
Our production, an unbeatable duo: state-of-the-art machinery combined with our expertise.
With 45 employees and an annual cut of 45,000 cubic metres, we are a medium-sized company. This gives us the advantage of being able to respond very flexibly to our customers’ wishes.
We specialise in quality timber made from silver fir and spruce. We use the latest technology to produce knot-free goods in a wide range of dimensions from high-quality strong logs.
From our location in the heart of the Black Forest, we supply customers throughout Europe and beyond.
How beautiful logs become even more beautiful products
in eleven steps.
First of all, each individual log is assessed by our log buyer for various qualities before it is accepted and purchased. After evaluation, the timber is delivered to the sawmill by log forwarders to the log yard or alternatively to the wet store.
Once the logs have arrived at the sawmill, they are placed on the debarking machine by our excavator driver. There, the logs are completely debarked. The debarked logs are then sorted and stored in a separate log yard or placed directly on the log bandsaw intake as required.
After debarking, the logs are sent to the log bandsaw. There, the log is first measured in 3D. The log is then cut (‘filleted’) according to its condition/quality and customer requirements in such a way that the best possible added value is achieved.
The cut timber is transported to the recutting line via a chain conveyor. There it is checked and assessed again by one of the employees before it is then trimmed and cut into the various raw dimensions.
We have a total of 46 of these sorting boxes. When one of these boxes is full, it is automatically emptied. The cut goods are visually checked again by an employee before they are stacked.
This is the first step in the wood refinement process. The sawn timber is gently dried in the drying chambers, which are supplied with heat from the company’s own power station, at temperatures of approx. 65°C to a residual moisture content of approx. 10% (+/- 2%). On the one hand, the wood is therefore free from pests and, on the other, our customers benefit from greater dimensional stability.
After drying, the sawn timber blank is first pre-planed. The wood then runs through our WoodEye wood scanner. This recognises the wood characteristics (e.g. knots, cracks, colour changes, structures) on all four sides and evaluates the optimum quality yield.
When the sawn timber is scanned, the cross-cuts are transmitted to the downstream cross-cut system. This means that any deviations such as knots, cracks etc. are cut out.
Scanning and cross-cutting also produces 20 – 80 cm cross-cuts, which are used for finger-jointing. These cross-cuts are first assessed again by employees and stacked according to quality. The cross-cuts are then placed on pallets or on the finger-jointing line by robots. Here, small wedges are milled into the two short sides of the cross-cuts, which are glued and pressed together in the next step. This creates new finger-jointed blanks up to six metres long, from which further products can be manufactured. In addition, finger-jointing gives us significantly higher added value.
The wood is shaped on our high-performance planing machine. Here we have the option of producing different profiles and can therefore respond even more specifically to customer requirements.
Depending on the product, we glue with D4 white glue or polyurethane glue. Among other things, we glue and press our finger-jointed products and our solid wood panels with D4 white glue. Our three-layer boards are glued and pressed with polyurethane glue.
On time and safe:
Our logistics.
To ensure that Echtle products are delivered on time and undamaged, we work closely with long-standing logistics partners.
We load numerous lorries with our sawn timber every week. Timber deliveries to Japan are loaded in containers.
Joint project Holzbauwerk Schwarzwald: new standards in CLT production.
Together with Holzwerk Kübler and Sägewerk Streit, Echtle forms HolzBauWerk Schwarzwald GmbH. If you add up our experience, you get 450 years that we use to set new standards in wood processing. Since autumn 2022, we have been producing highly refined timber components, cross-laminated timber (CLT), in a 13,000 m2 production hall in Besenfeld-Seewald in the district of Freudenstadt. This modern timber construction product made from sawn timber is multi-layered and completely solid. Its cross-lamination makes it extremely dimensionally stable – perfect for walls, ceilings and roofs.
Discover what HolzBauWerk can do at::
www.holzbauwerk-schwarzwald.de
STRUCTURE OF A THREE-LAYER PANEL hbwCLT
The Echtle company has developed from an agricultural business to a modern, innovative sawmill and planing mill with the latest production technology.
In 1890, Josef Echtle for the first time used the farming-wise unproductive winter months to make lumber and timber. The simple saw frame was powered by hydropower of the Nordrach river. A board hemmer was available to trim the slabs. While agriculture remained the main source of income for the family for many more years, but Josef Echtle, born in 1870, thus laid the cornerstone for the growth of a successful business that today employs 45 people in Nordrach.
Purchasing and operating the first frame saw in 1910 made it possible to saw larger logs, thereby increasing the cutting performance. At that time, the sawmill only employed family members. They produced all building materials that were needed in the area around Nordrach at the time: timber, roof batten, scantlings or planks. Back then, logging was the exclusive domain of the forestry administration. Logs would be placed by the side of the road and sawmill operators had to take care of transportation from there. Initially, that was done by using oxen and horses, they were later replaced by tractor-trailers.
One change occurred in 1919: Karl Echtle, only 18 years old then, took over company management. Local authorities in Nordrach declared him to be of full age early for that reason.
In World War II, the Echtle family had to pledge to deliver lumber to the Wehrmacht. This ensured full emplyoment and made it possible for the first time near the war’s end to take a big step into the age of technology: a hydraulic turbine was acquired. During the day, it also powered an electric skiving machine in the sawmill and in the evenings it provided the family’s home and neighboring homes with current. The purchase of the first tractor was a big relief, as it significantly facilitated transportation to and from the sawmill.
The year 1964 became another milestone in the sawmill’s history: Herbert Echtle of the third generation takes over the company. His investments in the expansion of the premises and the acquisition of a second frame saw as well as the purchase of the first fully automated logstacker in the area are visible signs of economic success. This expansion also meant the creation of new jobs.
Through continued automation (e.g. the setup of one of the first partitioning machines for logs in 1972), the sawmill could now grow its production volume annually. The increased demand for lumber in the Rhine-Main area was recognized early and the sales area was extended supraregionally for that reason. In 1974 the demand for dried and planed timber for interior fittings could be met through the construction of a new storage facility, a drying chamber and a planing machine.
From 1987, Manuel Echtle took over as managing director in the fourth generation. The two-frame sawmill with a capacity of 30.000 solid cubic meters of timber and dimension goods marked a break for the time and cutting edge technology-wise, but it was realized that the sawing industry underwent change and that either mass-market or niche production would be the future.
For this reason, it was decided in 1995 to build a new band sawmill with re-cutting machine and a sorting unit. Thus, next to the “old” sawing facility with two frame saws a new unit for the block bandsaw was constructed on the company’s grounds of a total 2.5 hectares, complemented with a timber sorting unit with 46 boxes in between the units.
From then on, the Echtle sawmill specialized in cutting logs. As the demand for lumber declined, quality timber was more sought-after. With that in mind, the frame saw facility and the log space were closed in 1999. In 2000, Echtle set up a facility to bark short timber and introduced a two-shift system in the bandsaw plant in order to retain both capacity and staff.
When the round log area was dismantled in 2001, it was decided to enter the field of processing and to set up a new workshop with 2800 sqm in the vacant spot. This new building and the installation of a state-of-the-art machine park it now became possible to process the high-quality timber, for example by fine-cutting, planing, finger-jointing or face machining it.
In the spring of 2003, the production line for manufacturing solid wood floorings made from locally grown silver fir was founded. The Baden-Württemberg minister of rural development, Willi Stächele, visited the company and learned about the vast capabilities of the factory; the first one capable of making solid wood flooring panels from fir.
n 2005, a slab press to manufacture branchless fir solid wood panels with joint-fingered or continuous slats was put into operation. At the same time, the Echtle sawmill demonstrates that it is committed to the preservation of the threatened silver fir, which is a vital guarantor to natural, ecologically important and storm-proof forests in the Black Forest area. For this reason, the Echtle sawmill is a partner in the FORUM WEISSTANNE (silver fir forum), a not-for-profit association that aims at the wide-ranging conservation of the silver fir.
Our slogan „Saw, dry, plane, cut, dovetail“ describes the range of our business activities as well as the path the timber follows through the sawmill: the round log space receives several thousand cubic meters of timber from the region’s forests per month. Every single log will be checked, as Echtle only works with immaculate qualities. In the next step, the logs are being sorted and placed in a block storage separated by type of wood and diameter classes. After barking, the cutting-edge bandsaw takes care of apportionment and finally the cutting of the logs. Then, the timber is sorted and stacked for processing. The finishing of products is done by mechanical wood drying, branch cutting, finger-jointing, planing, shaping and glueing. Our drying chambers with a total capacity of some 1000 cbm are operating around the clock.
With the construction of a biomass power plant in 2006/2007, the Echtle company entered the field of power production. Apart from a electrical power output of 900 kW, the power plant has a thermal output of 5.000 kW. By using spare wood, enough energy can now be produced to supply all of the drying chambers of the sawmill with heat for wood drying. In addition, the waste heat currently supplies some 250 households as well as two health clinics, public buildings and Nordrach’s public pool.
As fuel, bark and forest chips are being used, entirely natural fuels that only need to be milled mechanically. Half of the fuel comes from own production, the other half is purchased. The plant has an annual consumption of about 60.000 loose cubic meters of said materials.
Founding of HolzBauWerk Schwarzwald GmbH
Sawmills Echtle, Kübler, and Streit invest into the future with a CLT plant with industrial-style production. The new company goes by the name HolzBauWerk Schwarzwald GmbH, registered and located in Seewald-Besenfeld (Freudenstadt district).
In this company, highly refined component made from lumber will be manufactured here. Cross-laminated timber or CLT is a cutting-edge timber work product that is multi-layered, completely solid and made from lumber. Thanks to its cross lamination, it is extremely dimensionally stable and is very well suited for the construction of walls, ceilings and roofs.
Production started in autumn 2022.
Here you can find more information about HolzBauWerk Schwarzwald.
Renewal band sawmill
After 27 years of operation and over one million fixed meters, CEO Manuel Echtle decided to renew the band sawmill.
Mr. Echtle decided for a new band sawmill of the company EWD, with the latest and most modern technology. With this new band saw you can work even more efficiently and productively. The block band saw type EBB-2 divides hardwood into a variety of products – tailored to the needs of customers and the characteristics of the log on the jib.
This new band sawmill has been in operation since 26 October 2022. As a result, Echtle was able to switch from the usual two-shift operation to the one-shift operation.
Echtle is involved in the association for the sustainable promotion and conservation of silver fir. Find out more at www.weisstanne.info
The Echtle power plant fulfils the ISO 50.001 standard, a sustainable energy management system.
We are certified with the PEFC seal for wood products from sustainably managed forests.